Creating plastic pallets is a complex process that can be completed in a variety of ways. The design, material, and manufacturing process play a major role in how the pallet is constructed and its overall function. When choosing a transport warehouse plastic pallet mold, it is important to discuss with your manufacturer which options are most practical for your business.
One of the best options for producing plastic pallets is to use injection molding. This is a popular manufacturing method that is ideal for large-scale production. Injection molding involves high-pressure transfer of molten plastic into a mold. This process produces pallets that have a smooth, glossy finish. In addition to being easy to move, these pallets are also highly resistant to corrosion.
Another option for creating plastic pallets is to use a thermoformed process. In this method, the melted plastic is heated and stretched over a mold, resulting in a cellular structure in the core. This process is common in supply chain applications. The cost of this process depends on the type of plastic used and the blend of raw materials. It is a less expensive method than injection molding, which is why it is often used in conjunction with the latter.
While high pressure injection molding is the most commonly used plastic pallet mold, other processes are often used for different products. The most common types of thermoforming techniques include vacuum thermoforming and pressure thermoforming. Both methods have their advantages and disadvantages.
In the vacuum thermoforming process, a sheet of plastic is heated and forced into a mold, using a vacuum suction to help push it into place. However, this method cannot produce fine details. There are other options, such as structural foam molding, which is a low-pressure injection molding process. This method produces plastic pallets that are more lightweight and durable. It is a good choice for rigid plastic pallets.
The process also makes use of an inert gas, which expands inside the mold cavity to hold the pressure. This gas helps form a foaming reaction between the molten plastic and the mold. After the process is completed, the resulting pallet has dense walls and a cellular structure in the core.
This process can be used to create pallets that are able to withstand cold-chain supply procedures. It is also a good choice for food and pharmaceutical industries, since it increases sanitation.
In addition to being durable, these plastic pallets have the same dimensional accuracy and load ratings. This is important because they do not have sharp edges. Furthermore, they provide a cleaner working environment. They are also safer to handle in a dispatch area. They are not susceptible to splinters and nails, and are recyclable. They are also washable.
Thermoformed plastic pallets are available in a variety of sizes. They can be manufactured from recycled or virgin plastic. They are also available in twin-sheet, nestable designs. They are also available in standard sizes.
There are many advantages to using a transport warehouse plastic pallet mold. These include the ability to produce a variety of pallets in a single manufacturing process. In addition, they are more durable than wooden pallets. The process also helps eliminate the need for nails, nails and screws.
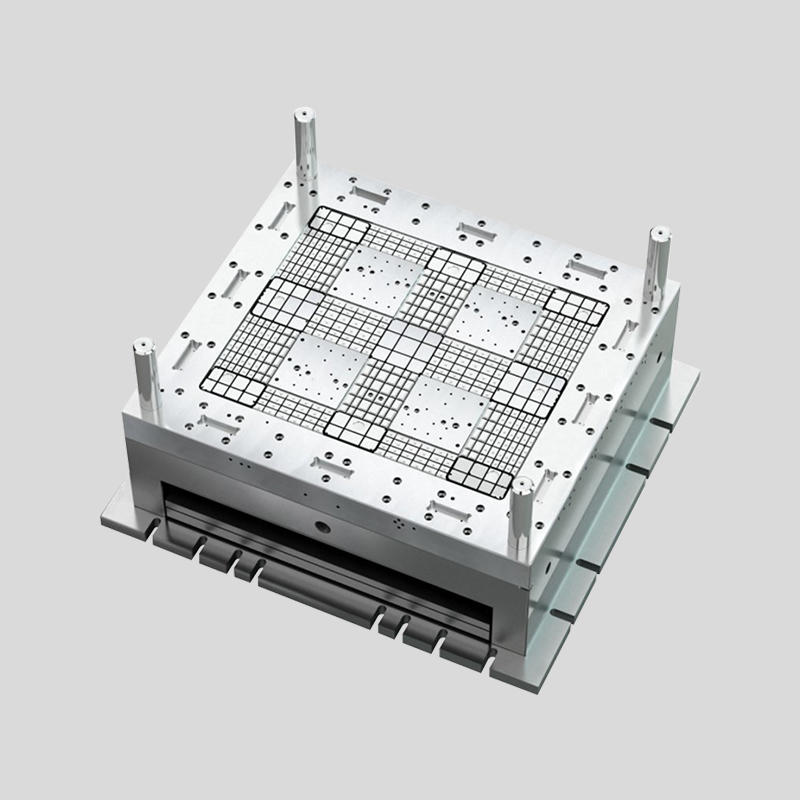