2. Design Flexibility: Plastic injection molding offers unparalleled design flexibility, allowing manufacturers to create complex and intricate product designs. The ability to mold plastic into virtually any shape or form opens up a world of creative possibilities. With injection molding, manufacturers can incorporate features such as undercuts, thin walls, and intricate details, providing enhanced functionality and aesthetics. This flexibility enables product designers to bring their innovative ideas to life and meet the evolving demands of consumers.
3. Rapid Production Cycles: Time-to-market is a critical factor in today's fast-paced manufacturing landscape. Plastic injection molding enables rapid production cycles, allowing manufacturers to quickly turn concepts into finished products. Once the mold is created, the injection molding process can produce parts or products in a matter of seconds or minutes. This rapid turnaround time enables manufacturers to meet tight deadlines, respond swiftly to market demands, and seize opportunities for new product launches or customization.
4. Consistent Quality: Plastic injection molding ensures consistent and high-quality production. The automated nature of the process reduces the likelihood of human error, resulting in uniformity in product dimensions, specifications, and characteristics. The ability to control and monitor key parameters such as temperature, pressure, and injection speed ensures repeatable and precise results. Consistent quality not only enhances customer satisfaction but also reduces the need for rework or product recalls, further enhancing manufacturing efficiency.
5. Material Variety: Plastic injection molding accommodates a wide range of materials, providing manufacturers with access to diverse material properties and characteristics. From commodity plastics to engineering-grade resins, manufacturers can select the most suitable material for their specific application. This versatility enables the production of products with varying strength, durability, heat resistance, chemical resistance, and other properties. The ability to choose from a vast material palette enhances product performance and allows for innovation in material selection.
6. Waste Reduction: Plastic injection molding contributes to waste reduction in manufacturing processes. The process generates minimal scrap, as excess plastic from the mold can be recycled and reused. Injection molding also allows for efficient material usage, with the ability to precisely control the amount of plastic injected into the mold. The reduced material waste not only improves sustainability but also reduces production costs associated with material disposal and waste management.
7. Integration with Automation and Industry 4.0: Plastic injection molding aligns well with automation and Industry 4.0 initiatives. The process lends itself to integration with robotics, automated part removal, quality inspection systems, and data collection sensors. Automation streamlines the production process, enhances efficiency, and reduces human intervention. Additionally, injection molding machines equipped with IoT capabilities can gather real-time production data, facilitating process monitoring, predictive maintenance, and continuous improvement efforts.
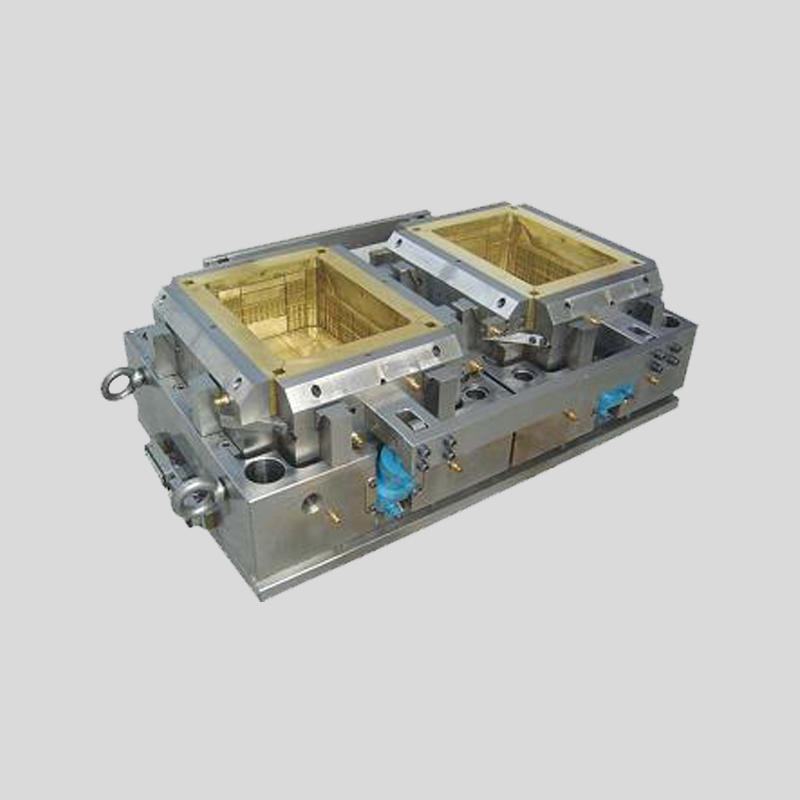