During the process of injection molding, a material is packed into the mold while it holds pressure. This process is called the V-P switch-over, and the materials must be in an appropriate proportion. In the case of plastics, it is best to fill mold cavities almost completely during this phase. The plastic will then solidify and attach to the part. Once the part has been created, post processing is required to clean and finish the part.
For industrial applications, 3D printing is an excellent option for manufacturing an injection mold. It requires minimal equipment and eliminates the need for CNC work and skilled operators. In-house 3D printing enables manufacturers to quickly produce a mold for industrial or desktop machines, and it enables product development to iterate on the design as the process continues. Injection molding with stereolithography (SLA) technology allows companies to save time and money by avoiding costly and labor-intensive manufacturing processes.
The hopper of an injection unit heats the raw plastic material that goes into the mold. The hopper is open at the bottom and feeds the plastic material into the barrel. The barrel is equipped with a heating mechanism. The ram injector forces the material forward through the heated section. The reciprocating screw is more common than the ram injector, and it is also more efficient. The ejector bar actuates the ejector system, which pushes the solidified part out of the open cavity.
Injection molds are highly precise and accurate. They are better suited for complex designs and detailed shapes. Injection molds are typically subjected to high pressure and high temperatures, resulting in plastics that are pressed harder. This allows for more detail and complex designs. It is important to understand how these processes work. It is critical to know how to design an injection mold. It can be designed to fit a particular application.
Injection molds are used to create plastic parts. The plastic in an injection mold is made of two components - the A-side and the B-side. The A-side of an injection mold will hold the part while the B-side is closed. This is the reason why an object needs to be fully filled with plastic before it is injected into the mold. This way, it is possible to achieve the desired shape without causing any complications during the injection process.
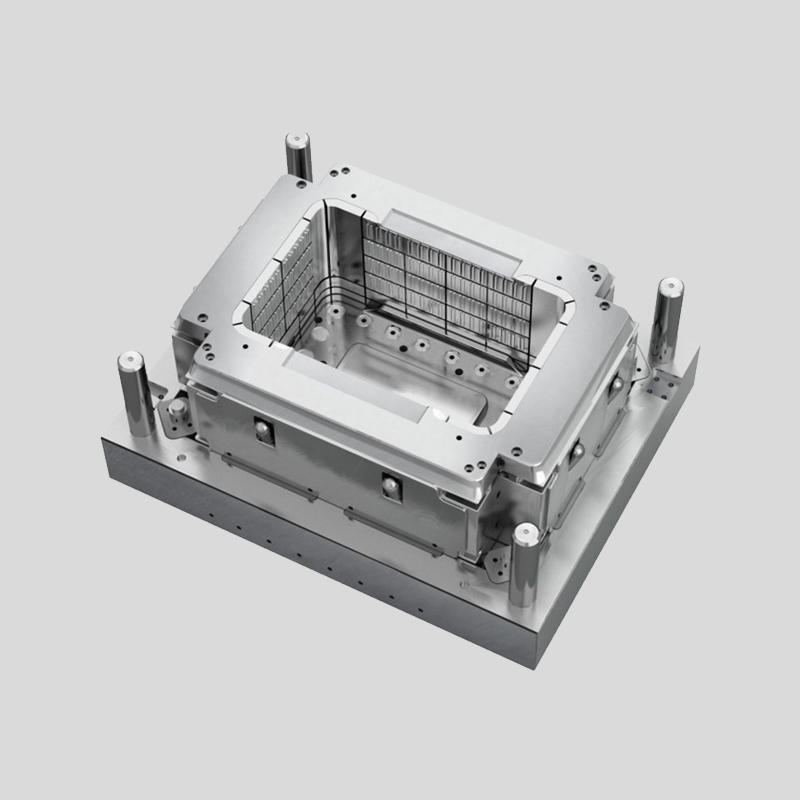