Plastic pipe is manufactured in an injection molding machine. Molten plastic is fed into a die by an extruder and cooled in water or coolant. This process creates a flange, or hub, at the end of the plastic pipe. Once the pipe is cooled, it can be ejected from the mold.
PVC pipe fittings have many different uses. They are used in the production of various products in the automotive and home appliances industries. They are also used in vacuum cleaners and other home appliances. In the United States, PVC is commonly known as vinyl. In Europe, the material is mostly used for flexible applications, including flooring and artificial leather. The cost of PVC pipe fittings is lower than the cost of metal pipe fittings. They are also waterproof and lightweight.
PVC is a highly flexible plastic that is typically molded in an injection molding machine. This material can be processed at temperatures between 100oC and 260oC. It is often mixed with additives to achieve various physical properties, which can be useful in many different applications. For example, PVC can be used to make electrical socket covers and flexible films.
When it comes to designing a mold for PVC pipe fittings, you'll need to pay attention to the details. Unlike simple solid structures, PVC pipe fittings can be quite complex and require multiple parts. If you want to produce PVC pipe fittings of a high quality, it's important to choose a mold that is made from the right material.
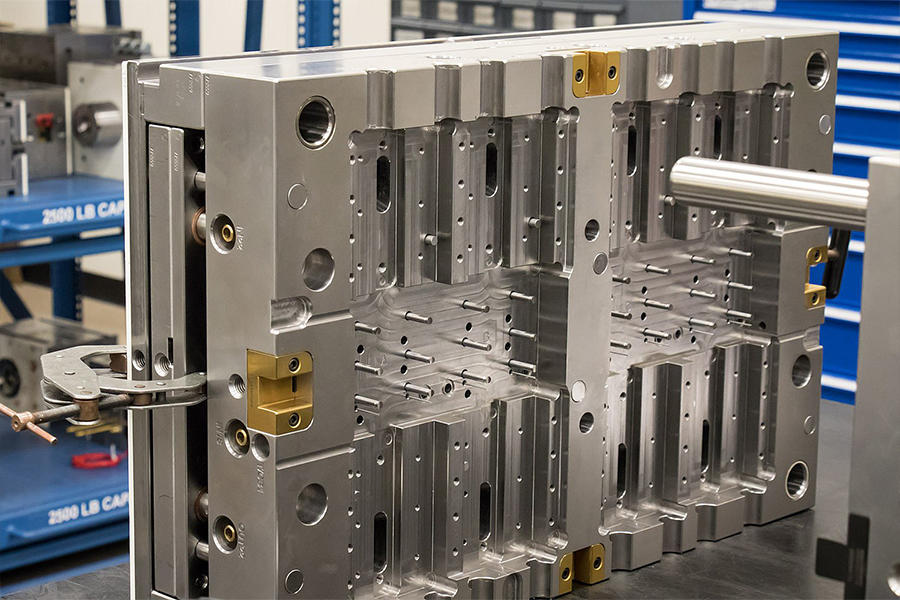