2. Design Flexibility: Commodity molds offer a certain level of design flexibility, allowing for the production of standardized components with minor variations. These molds can accommodate multiple variations of a product design, such as different sizes, shapes, or features. This flexibility enables manufacturers to cater to a broader market with minimal modifications to the mold design.
3. Lead Time: Lead time is an essential factor in manufacturing operations. Commodity molds, being standardized and readily available, significantly reduce lead times compared to custom molds. Manufacturers can quickly procure commodity molds and initiate production, resulting in faster turnaround times and improved operational efficiency.
4. Tooling Durability: Commodity molds are typically constructed with durable materials and robust construction techniques to withstand the high-volume production demands. The durability of these molds allows for repeated use over an extended period, minimizing the need for frequent mold replacements and reducing overall tooling costs.
Benefits of Commodity Molds:
1. High Production Efficiency: Commodity molds are optimized for high-volume production, making them highly efficient for manufacturers. The molds are designed to achieve fast cycle times and consistent part quality, enabling manufacturers to meet demanding production schedules and maximize output. This efficiency is particularly advantageous for industries with high-demand products or tight production deadlines.
2. Cost Savings: The use of commodity molds can result in significant cost savings for manufacturers. As mentioned earlier, the economies of scale associated with commodity molds lead to lower production costs per unit. Additionally, the reduced lead time, durability, and reusability of these molds contribute to overall cost savings in terms of mold maintenance, replacement, and tooling expenses.
3. Standardization and Interchangeability: Commodity molds allow for the production of standardized components or parts that can be easily interchanged or integrated into various end products. This standardization simplifies inventory management, assembly processes, and aftermarket servicing. Manufacturers can achieve economies of scale by producing components that are compatible with multiple product lines, reducing complexity and costs associated with customized or unique molds.
4. Scalability: Commodity molds provide scalability options for manufacturers. The standardized design and availability of these molds enable manufacturers to quickly scale up production in response to market demand. This scalability allows manufacturers to seize market opportunities, respond to customer needs promptly, and adapt to changing business conditions effectively.
5. Quality Control: Commodity molds, when designed and maintained properly, can contribute to consistent part quality. The repeatable and controlled nature of the molding process, combined with the durability of the molds, ensures consistent product dimensions, tolerances, and surface finishes. This consistency enhances overall product quality and customer satisfaction.
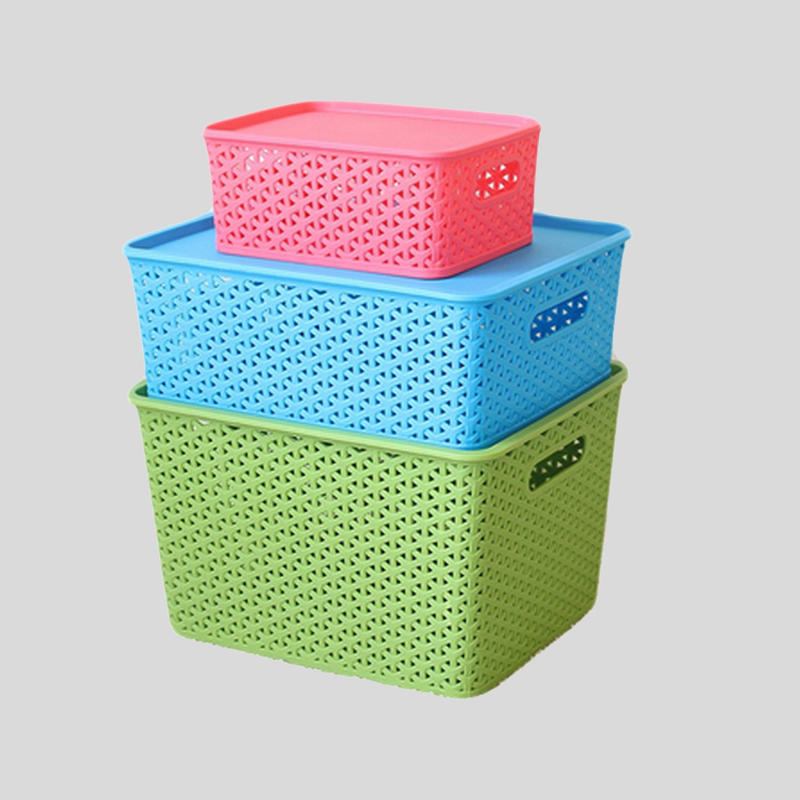