Plastic molding is a versatile and efficient manufacturing process that allows the creation of complex, custom, and precision components with relative ease. It typically involves the following key steps:
Material Selection: The process begins with the selection of a suitable plastic material, often in the form of pellets or granules. The choice of material depends on the specific properties and requirements of the final product.
Melting: The plastic material is heated to a liquid state within a specialized machine called an injection molding machine. The heat softens the plastic and prepares it for shaping.
Injection: The molten plastic is injected into a mold cavity under pressure, allowing it to take on the desired shape. The mold itself is often made from metal and designed to be precise and durable.
Cooling: After injection, the mold cools the plastic, causing it to solidify and retain the molded shape.
Ejection: Once the plastic has cooled and solidified, the mold opens, and the finished product is ejected.
Common Plastic Molding Techniques
Injection Molding: Injection molding is the most widely used plastic molding technique, favored for its high production efficiency and precision. It's ideal for producing a wide range of products, from small and intricate parts to larger, more complex items such as automotive components and medical devices.
Blow Molding: This technique is commonly used for creating hollow plastic products such as bottles, containers, and plastic drums. It involves inflating a heated plastic parison inside a mold to give it its final shape.
Rotational Molding: Rotational molding is a method used for producing large, hollow objects like water tanks, playground equipment, and storage containers. The plastic is heated within a mold that rotates in multiple axes, allowing for even distribution and shaping.
Compression Molding: Compression molding is suitable for high-strength, high-temperature plastics. It's often used to manufacture items like brake pads, electrical connectors, and appliance components. The plastic material is placed in a heated mold, and pressure is applied to compress and shape it.
Applications of Plastic Molding
The applications of plastic molding are diverse and vast, making it an indispensable process in today's manufacturing landscape. Some key areas where plastic molding plays a crucial role include:
Consumer Products: Many everyday items like toys, household appliances, kitchenware, and packaging are produced using plastic molding techniques.
Automotive Industry: Plastic molding is widely employed in the automotive sector, where it's used to manufacture various parts, including bumpers, interior components, and intricate engine components.
Medical Devices: The medical field relies on plastic molding for the production of devices such as syringes, medical implants, and diagnostic equipment.
Electronics: The production of casings, connectors, and other components for electronic devices often involves plastic molding.
Aerospace: The aerospace industry utilizes plastic molding for creating lightweight, durable components and interior parts for aircraft.
Construction: Plastic molding is used to manufacture pipes, fittings, and other construction materials.
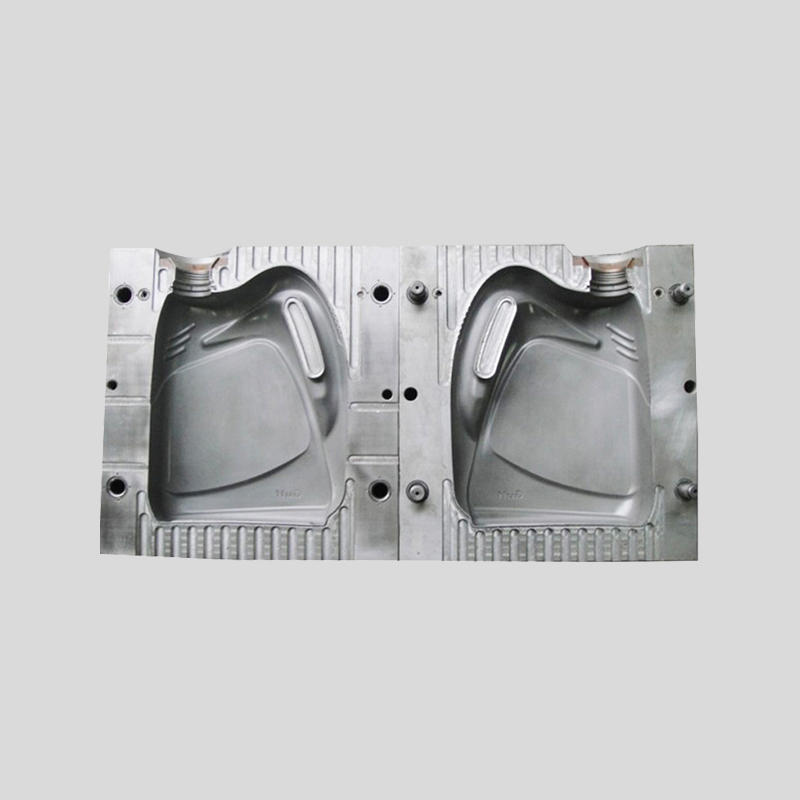