Accrylonitrile butadiene styrene (ABS) is a plastic commodity mould
ABS, or Acrylonitrile Butadiene Styrene, is a thermoplastic polymer. It is durable and easy to machine. Its high impact strength and low cost make it suitable for mould-making and other industrial applications. However, its lack of chemical resistance, fatigue resistance, and UV resistance make it unsuitable for high-stress applications.
Polycarbonate is a clear plastic
There are several advantages of using polycarbonate as a mold material for plastic products. Its process is highly efficient, allowing for a rapid cycle time and a large variety of mould sizes. Tolerances are also an important consideration in polycarbonate parts and the moulding process helps in maintaining that tolerance. Here are three benefits of using polycarbonate as a mould material:
Polyethylene is a semi-crystalline plastic
The term "polyethylene" is derived from the Greek words polymeros, which means "many." This resin is composed of many small molecules that are linked together to form long polymer chains. Polyethylene's chemical properties depend on the size and orientation of these molecules. It has excellent mechanical, chemical, and wear resistance. This material is nonconductor, lightweight, and stain-resistant. It floats in water.
Polypropylene is a thermosetting plastic
As a thermosetting plastic, polypropylene is a material that can be processed to produce a variety of plastic products. This versatile material is widely used in household products, including plastic bottles, thermoplastic underwear, and ropes. Due to its low electrical conductivity, polypropylene is a useful material for electronic applications. You probably have at least one piece of polypropylene in your home.
Polyethylene is an eco-friendly plastic
Polyethylene, also known as polypropylene, is a common plastic used in the production of everyday items. Its crinkly nature makes it a desirable material for packaging because it does not stretch or rip easily, unlike HDPE. The material is also resistant to corrosion, chemicals, and other elements. This means that recycled products can be mixed with virgin ones when moulding a plastic commodity.
Polyethylene is a clear plastic
The most common type of consumer plastic is polyethylene. It is used for a wide range of everyday products, such as bottles and plastic bags. The plastic is thermoplastic, meaning it can be heated to liquid form and cooled to solid form. Different grades of polyethylene are produced depending on the processing conditions. Each grade is used for a specific purpose. This article provides an overview of each type. Polyethylene has many advantages.
Designing a plastic commodity mould
One of the challenges faced by design engineers is determining the right locations for gates. Gates are openings in a mould that direct molten plastic into the mould cavity. Gate locations and types depend on the design of the plastic part and the type of resin being used. Design engineers must consider factors such as fill pressure, mold cooling time, and part dimensions/tolerance before deciding on gate locations and types. The location of the gate must not negatively affect the part performance, but should be designed to meet the manufacturer's specifications.
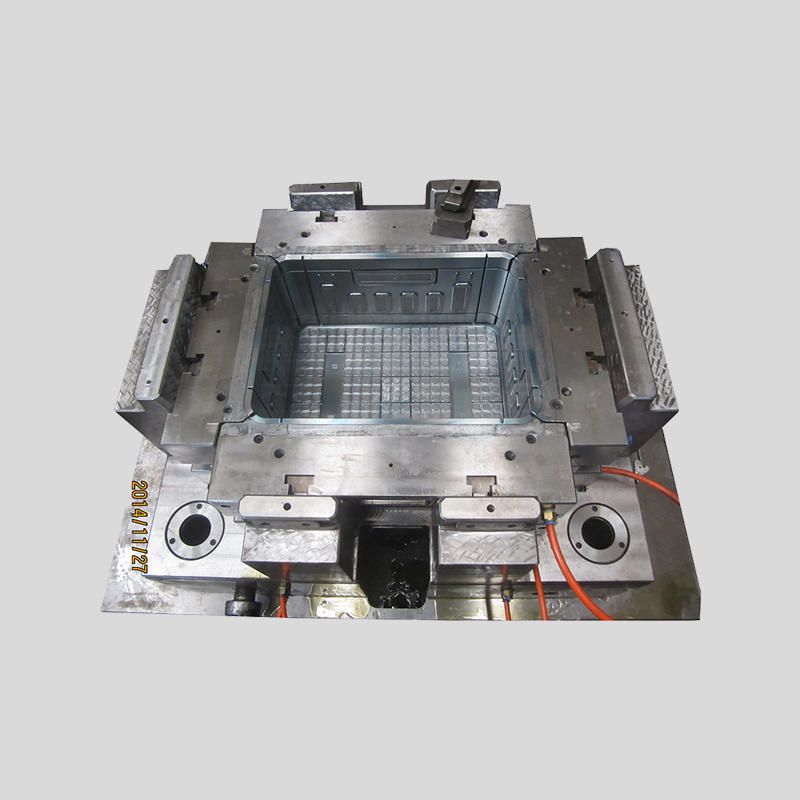