Blow plastic molds are instrumental in the manufacturing of hollow plastic objects, ranging from bottles and jars to containers of various shapes and sizes. They are crafted from durable materials such as aluminum, steel, or high-grade alloys, meticulously engineered to withstand the rigorous demands of blow molding operations.
The primary function of blow plastic molds lies in their ability to shape and mold plastic materials into specific designs. Utilizing the blow molding technique, these molds facilitate the creation of hollow plastic containers by inflating heated plastic into the desired shape within the mold cavity. This process ensures uniformity, precision, and consistent quality in the final products.
One of the key advantages of blow plastic molds is their versatility in producing containers with diverse designs and functionalities. Whether it's intricately shaped bottles for beverages, containers for personal care products, or automotive components, these molds offer flexibility in creating custom designs to meet the unique needs of different industries.
blow plastic molds cater to various plastic materials, including polyethylene terephthalate (PET), polyethylene (PE), polypropylene (PP), and more. This adaptability allows manufacturers to produce containers with different material properties, such as transparency, flexibility, or durability, tailored to specific product requirements.
Efficiency and cost-effectiveness are significant benefits offered by blow plastic molds. Their ability to create complex shapes in a single-step process minimizes production time and reduces manufacturing costs. The streamlined production cycles ensure higher output rates, meeting market demands more efficiently.
these molds are engineered for durability and longevity. They undergo stringent design and testing processes to withstand the high pressures and temperatures involved in blow molding operations. The robust construction of the molds ensures prolonged service life, contributing to cost savings for manufacturers.
blow plastic molds are at the forefront of sustainability efforts in the plastic packaging industry. Innovations in mold design and process optimization aim to reduce material wastage, energy consumption, and environmental impact. The shift towards lightweighting containers and the ability to produce thinner walls with these molds contribute to overall sustainability goals.
As technology advances, ongoing innovations in blow plastic molds are expected. Manufacturers continue to explore new materials, design improvements, and advanced technologies to further enhance efficiency, precision, and sustainability in plastic container manufacturing.
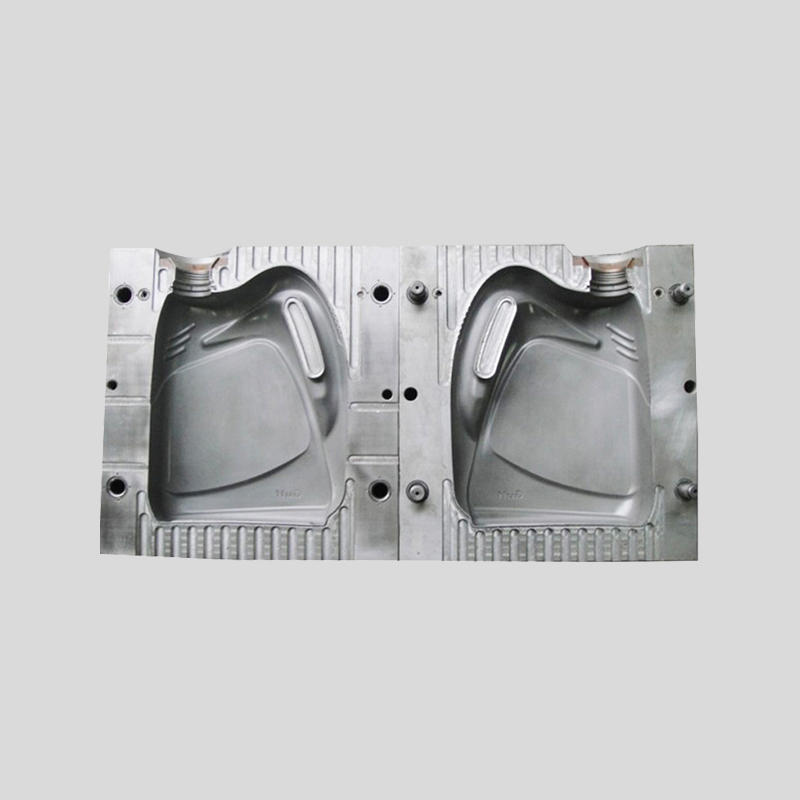