Blow molding is a manufacturing process used to create hollow plastic parts. This technique involves melting plastic resin and forming it into a hollow tube, commonly known as a parison. The parison is then placed within a mold cavity where air is blown into it, causing the molten plastic to take the shape of the mold.
Blow plastic molds are meticulously designed structures that determine the final shape, size, and intricacies of the plastic product. These molds come in various configurations, catering to diverse production requirements, and can be crafted from materials like aluminum, steel, or other alloys, depending on the desired outcome and production scale.
The Versatility of Blow Plastic Molds
One of the standout features of blow plastic molds is their versatility. They are utilized in the production of a wide spectrum of products, ranging from simple containers to complex automotive components. Their adaptability allows for the creation of items varying in size, shape, and intricacy, meeting the specific needs of different industries.
In the packaging sector, blow molds are instrumental in crafting bottles, jars, and containers used for storing various liquids and solids. The molds' ability to create different neck and body shapes ensures the suitability of the containers for diverse products, while maintaining structural integrity and aesthetic appeal.
blow molding plays a crucial role in producing components such as air ducts, fuel tanks, and even interior parts. The molds enable the creation of lightweight yet durable parts that meet stringent quality and safety standards.
Efficiency and Cost-effectiveness
Blow plastic molds excel in efficiency and cost-effectiveness, making them a preferred choice for manufacturers. The process allows for the rapid production of large quantities of uniform products with minimal material waste. The ability to create hollow parts reduces material usage, resulting in lighter products that require less raw material and are more economical to transport.
the production cycle of blow molding is relatively quick, ensuring high output rates. This efficiency translates to cost savings and increased productivity for manufacturers, contributing to their competitiveness in the market.
Advancements in Technology
The realm of blow plastic molds has witnessed significant technological advancements, enhancing their precision and capabilities. Computer-aided design (CAD) software enables precise mold designs, ensuring intricate details and consistent product quality. Innovations in materials and mold manufacturing techniques have led to increased durability and prolonged mold lifespan, reducing maintenance costs.
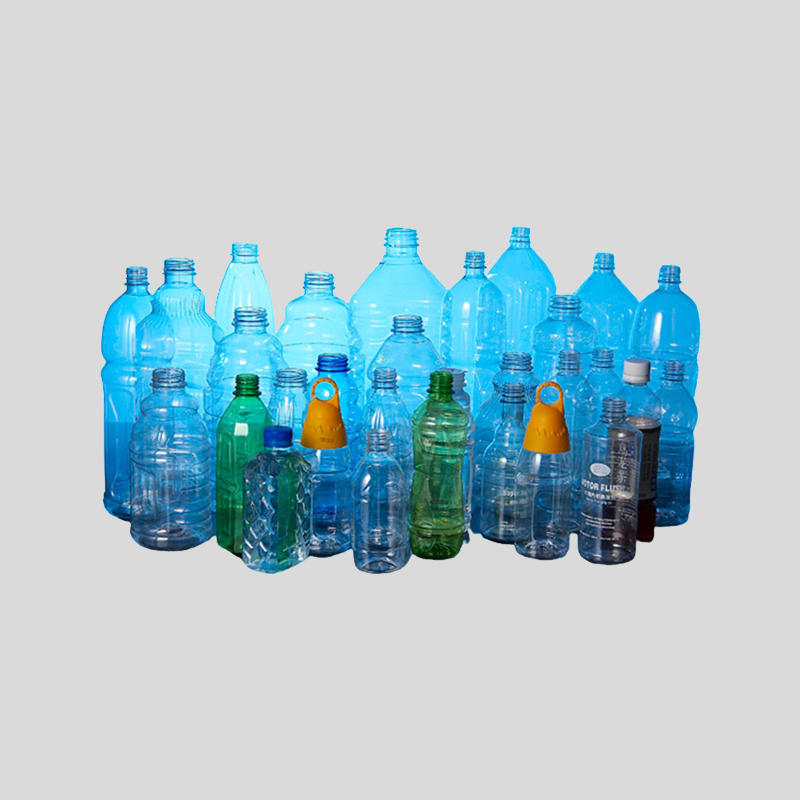