A mould is made by using a plastic resin and can imitate a wide variety of engineering grades. Its process uses a high temperature to ensure good strength and durability in the end product. It's also an eco-friendly option for producing large hollow parts. The downside of a plastic box mould is that it's not reusable. Even if you don't need a mold to produce several copies, it will degrade after about 20 copies.
Plastic box moulds can also be created using the process of extrusion moulding. This process uses a hot melted plastic to be pressed through a mould that is shaped like the shape of the part. This process can produce large quantities of plastic products, but the moulds themselves can be expensive. The cost per part decreases dramatically when the production volume increases. However, tooling can take up to 16 weeks before production is complete.
Rotational molding is a highly efficient process that produces few wastes. Excess material is often recycled or used for another product. It's also an environmentally friendly option, reducing both start-up costs and unplanned downtime. With these benefits, plastic box moulds are an excellent option for a variety of applications. So, if you're looking to create a unique packaging solution for your products, don't delay - find a plastic box mould today!
Plastic box moulds can be used for several different applications. There are also special plastic moulds for vegetables, beverage boxes, and other types of boxes for daily and industry use. If you're looking for a mould that works best for you, Taizhou Saiweiyue Mould & Plastic Co., Ltd. is the perfect place to turn to for your next project. When choosing a mould, make sure you consider its purpose and the material that you'll be moulding.
Injection molding, on the other hand, uses a mold to create custom parts. In this process, molten plastic is injected under high pressure into a metal mold and is cooled once it is in place. The process is similar to making a Jello mold, but unlike that, the plastic is solid, and the mold is reusable. The mold can also be changed at any time by a software engineer. A good mold manufacturer will have a tool room and wide range of machines to make it as precise as possible.
Extrusion molding is a popular technique for producing inexpensive containers. It requires easy tools and fast processing, but is not the best choice for high precision or complex parts. In this process, a molten plastic is injected into a cavity between two halves of a mould. Once it has cooled, the plastic takes on the shape of the mould. It will be cooled, and then ejected. You'll be able to use the plastic box mould to make containers of various sizes and shapes.
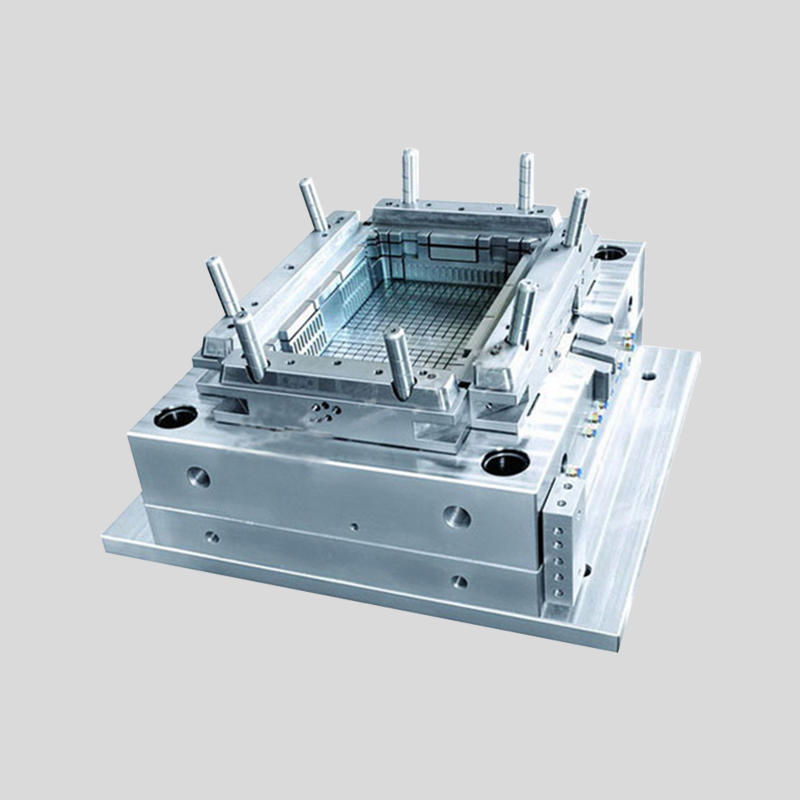