The automotive industry has traditionally been associated with metals and steel, but plastics are becoming increasingly popular as materials for automobiles. Plastic is more durable than metal, making them an ideal option for car manufacturers. Customers today have higher expectations for their vehicles, and plastic automotive injection molding is meeting those expectations better than ever before. To learn more about the benefits of automotive plastic injection molding, visit https://www.dhplasticmold.com/
Injection molding is a proven production method that produces complex plastic parts. This process involves injecting molten plastic into a mold cavity. The molten plastic then hardens and is then extracted. While the process requires precise precision and careful execution, the benefits of injection molding make this a highly reliable method for manufacturing solid plastic parts. This article will show you how injection molding works. And why you need to hire a professional mold-maker.
Injection molding is a common way to create interior parts for cars. Plastic injection molding produces dashboard faceplates, door handles, glove compartments, air vents, and more. The process is scalable, meaning the costs go down as more parts are produced. Injection molding is compatible with a variety of plastics, including ABS, polypropylene, acrylic, acetal, nylon, and polycarbonate. If you are making more than one or two components a day, you will likely find a mold that suits your needs.
If you want your automotive parts to stand out, branding is an important marketing tool. You can create a high-impact brand name and logo by integrating branding into your mold. You may want to consider using a process called insert molding, or even overmolding. You may also choose to make inserts from a non-plastic material. With the right technique, you can make your brand stand out among competitors.
For automotive parts, polyethylene and PVC are excellent choices. They offer durability, low density, and high impact resilience. They are both used in interior trim, battery covers, and electrical insulators. In addition to ABS and PMMA, automotive plastic parts manufacturers use PP for high-intensity components, such as the battery cover. Both of these materials are resistant to water and chemicals. You should check the quality of your mold before you purchase it to avoid wasted resin and labor.
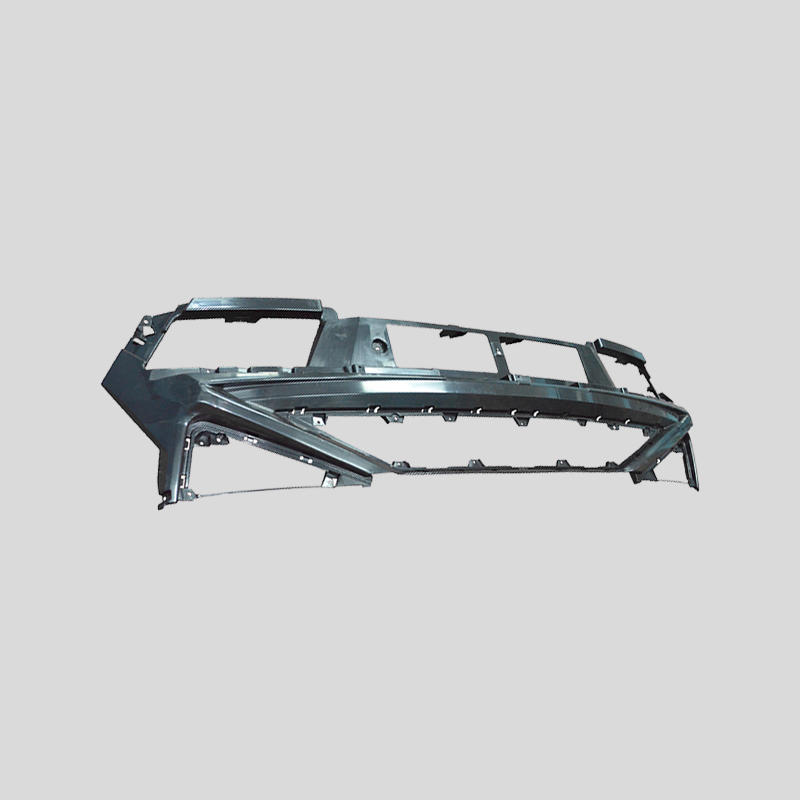