The shape of the molded plastic pallet is important to the strength of the product. Injection molded pallets are often shaped with ribs on the base of the mould. This ensures that boxes and other products are securely stacked. This type of pallet is an excellent choice for transportation of glass.
The ejection pin must be firmly connected to the insert. This helps to produce a smooth fit. It is also important that the ejection pin is surrounded by rods that help to generate an even force. The ejection pin should be as close to the insert as possible to avoid excess deformation.
The temperature of the core and cavity must be determined experimentally. This will be important to ensure proper crosslinks are formed in the resin. Thermocouples were used to measure the temperature of the core and cavity. The temperature of the cavity was determined to be around 55 degC, while the core temperature was around 20 degC. This was insufficient to transfer the heat to the cooling channel.
The core and cavity temperatures were measured with K type thermocouples. This was done to determine whether the thermal stress of the plastics was sufficient to induce shrinkage in the mold. However, shrinkage in the mold was not determined during the forming process.
The shrinkage rate of the same material is not the same in different molding factories. This is due to the different forming conditions and the mold structure. The unbalanced filling of the tool may also be a problem. In the future, DKM intends to apply micro-cell foaming technology to the plastic pallet mold to make the product more durable. The resulting pallets will be lighter and cheaper.
The simulated height of the pallet shows a deviation of 0.84 mm from the experimental profile. This is the largest deviation between the numerical and experimental profiles. This indicates that the flow front is extending to the four corners of the pallet.
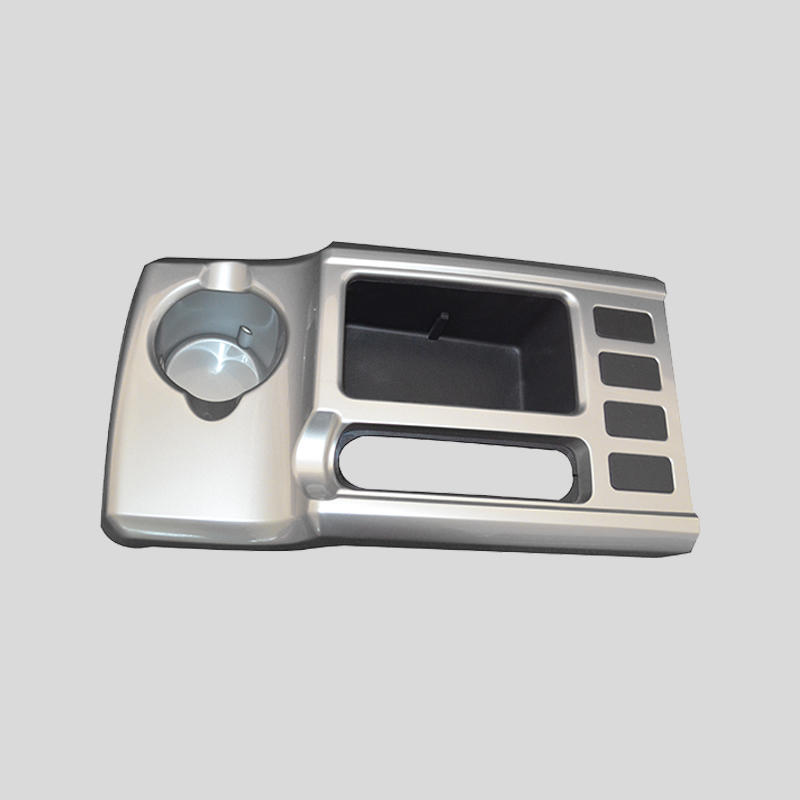