The plastic injection molding process uses a variety of polymers. The choice of materials can affect the final surface texture and finish. For instance, ABS plastic is an ideal material for the headlight cover application. It is also resistant to water and chemicals. Compared to steel, it can be molded more easily.
Injection molding is a reliable manufacturing method for making solid plastic parts. It can mass-produce thousands of identical products with low error rates and high surface quality. The process is also environmentally friendly. It is especially useful for replacing heavy metal parts in vehicles, which reduces operational costs and emissions.
Injection molding is a fast and efficient way to produce plastic car parts, which can help speed up the vehicle development cycle. As a result, the cost per unit decreases dramatically with production volume. The process can also be used to manufacture parts that need to be in contact with a variety of surfaces, such as interior components.
The plastic injection molding process includes a number of steps, including mould design, a 3D prototype, and injection of molten plastic. The best parts are made from high-quality materials and have tight tolerances. However, poor tooling and design can lead to defects. Moreover, redesigns may require additional money. In addition, the process can take longer than expected, as well as carry higher upfront costs.
The injection molding process is considered the best method to make precision high-quality plastic automotive parts. Injection molding produces a variety of parts, including bumpers, dashboards, and fenders. This manufacturing process also helps reduce the environmental impact of producing the parts. This type of molding is also highly scalable, so it can be used for a variety of applications.
The injection molding process is also ideal for producing flexible and rigid plastics. Some of the most common types of plastic used in the automotive industry are polypropylene and polystyrene. They are both weather-resistant and strong, and are commonly used for exterior car parts. Some manufacturers even use foamed polypropylene, which gives the parts a high degree of flexibility.
The automotive industry has also developed technology that makes it possible to convert metal parts into plastic. This process increases fuel efficiency and allows manufacturers to meet emission requirements. It is also more environmentally-friendly than other forms of manufacturing, because it uses less energy.
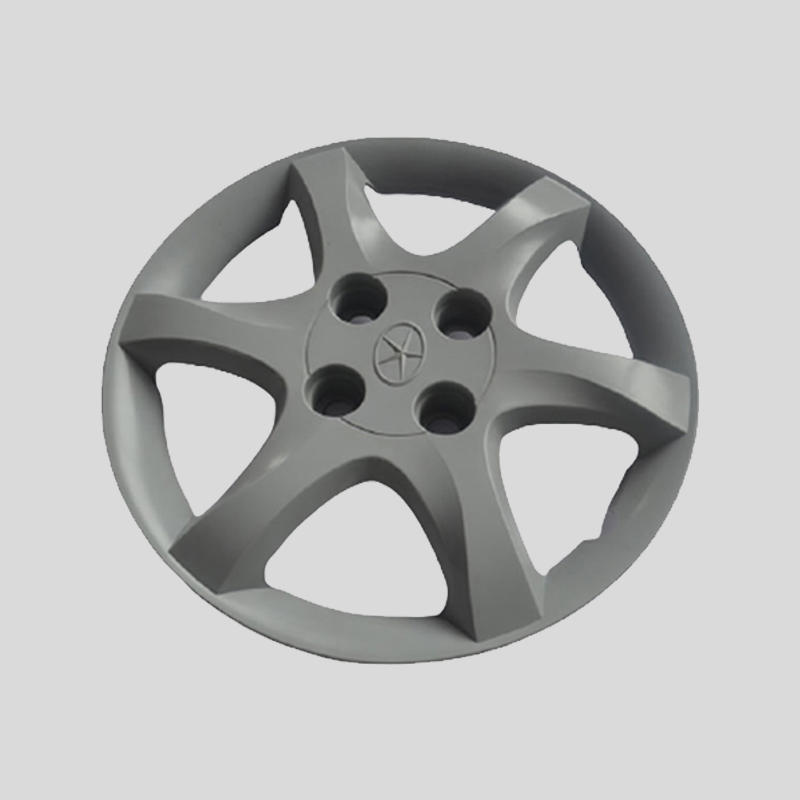