A mold is created by putting material into a cylinder. The resin is heated until it melts and is forced through the nozzle of the injection unit. The injection process uses a sprue or a branched runner to guide the material through the mold. The plastic is then molded into the desired shape. This process can be repeated many times. Once the plastic is molded, it is removed from the mold.
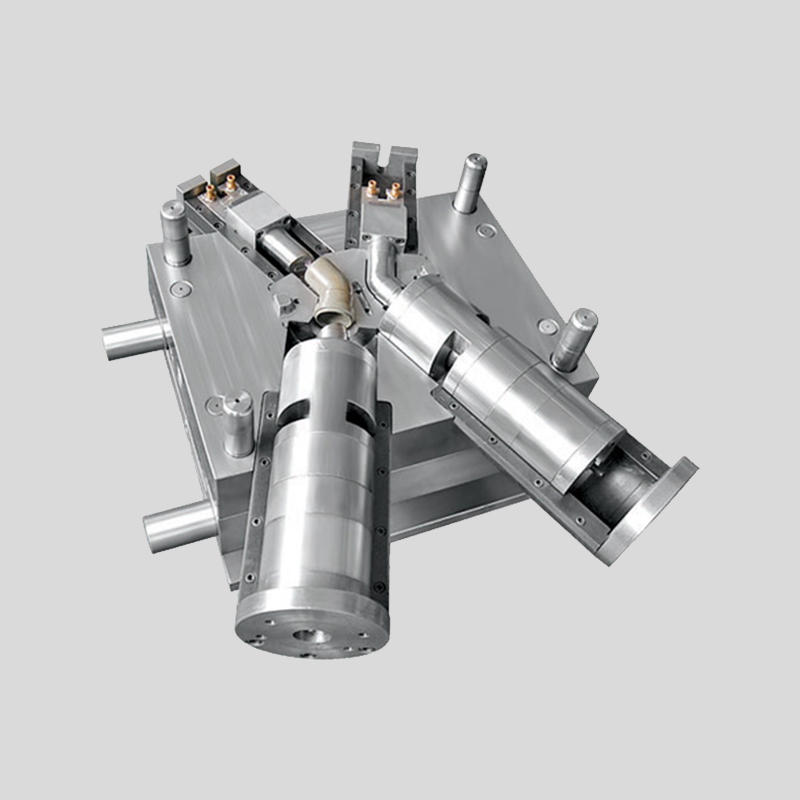
Once the plastic part has been placed into the mold, it can be released by pulling apart the two mold halves. In some cases, an ejecting rod or pin is used to release the part from the mold. The ejection process can take seconds to minutes. Injection molded products usually do not need secondary processing, but if the finished product is prone to imperfections, it may require additional steps to remove these imperfections. The amount of finishing depends on the material and the quality of the cavity.
When the plastic is ejected from the mold, it forms a smooth surface and is usually sanded. For some special applications, specialty coatings may be applied to the parts. The material is usually a thermoplastic such as high density polyethylene (HDPE), which is inexpensive and versatile. It is also waterproof, resistant to microbial growth, and chemically resistant. Another popular thermoplastic is polypropylene, which is a rigid crystalline thermoplastic valued for its electrical and chemical resistance. It is lightweight, bears stress, and is incredibly strong.
The most common type of injection molds are a cylinder with a stationary platen and a moveable platen. When the molten plastic is fully cooled, it solidifies and begins to shrink. While this can be an undesirable outcome, a refracting injection mold is a great option because it allows more material to flow into the cavity. This process will result in the most durable and long-lasting product.
Once the plastic is melted, it is injected into the mold cavity. The nozzle is the feeding system that delivers the resin to the mold cavity. When the resin pellets are pushed through the mold, they will be forced through the sprue or branched runner to the part. When the part is fully molded, it will be placed on a holder. This will prevent it from falling out of the injection cylinder.