One of the first steps in creating an injection mold is choosing a material that will stand up to the process. Plastics that are not designed for injection molding can cause a lot of problems, including flying material chips, volatile lubricants, and loose parts. This makes it imperative to choose a material that is able to withstand the process. For example, ABS or PP are two materials that can have very different properties.
An injection mould needs to be able to accommodate the different materials used in an injection process. The material must be resistant to the injection molding process. A poorly lubricated mold will cause a lot of problems. The wrong material can cause the process to fail. It's also important to choose the right type of material for the mold. A high-quality mold will last for many years. And while this may seem like an investment, it's an investment in your business.
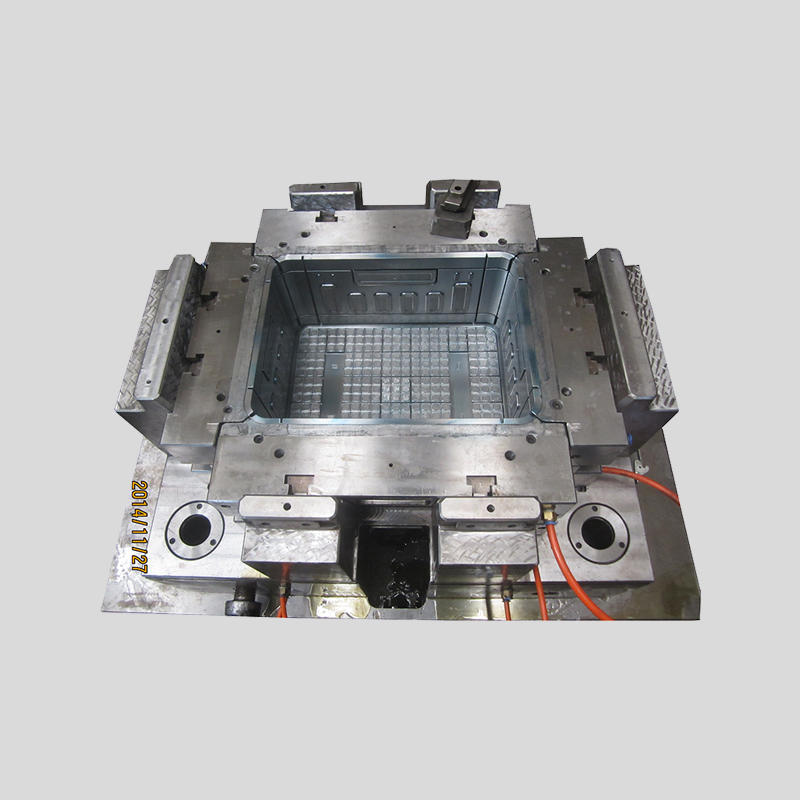
A good material is essential for an injection mold. The material needs to be able to withstand the injection molding process. In this step, plastic is packed into the mold cavity. The pressure is then held at that point. The plastic will start to harden once the V-P switchover occurs. For an effective injection process, the plastic mold should be nearly full. If the material is too dense or too loose, it will not be able to hold the desired shape.
Various factors can cause an injection mold to overheat. A poorly lubricated injection tool can result in overheating, which can lead to failure. A faulty heater can also cause overheating. An injection speed that is too high can cause an overheated tool. If the material is not thoroughly mixed, the masterbatch may not mix. A poor lubricated injection mold will cause the material to overheat.
After the injection molding cycle, post processing is necessary. The material solidifies and attaches to the part. A plastic grinder, also known as a granulator, will grind the trimmings to pellets. To reuse the plastic, the material must be injected with a high-quality lubricant. An injector can produce up to two parts of a mold per cycle. If the resin is too hot, it may lead to overheating, and can even cause problems.
A faulty injection mold can also cause problems. A badly-lubricated injection mold can be prone to overheating. Injection speed is too high. The masterbatch is not properly mixed. A poorly-lubricated injection mold will be weak. A badly-lubricated injection mould will result in a weak composite. To avoid this, it is essential to check that the lubricant is a good match.
Injection moulding is a process that uses polymers to create components. These include thermoplastics, thermosets, and elastomers. Since 1995, the number of materials available for this process has increased by 750 per year. There are now over a thousand materials available. The list of these materials is constantly growing. Some of them are alloys or blends of previously developed materials. The selection of the material should be based on function and strength.
An injection mould is a tool used to produce plastic parts. It is a machine that uses a heated barrel to melt the raw plastic. Injection units usually use a reciprocating screw or a ram injector to force the raw material through the heated section. During an injection process, the raw plastic is poured into a hopper with an open bottom. The hopper then feeds into the barrel which contains the heating mechanism.
There are three basic types of injection moulds. Each type can be built to meet a particular requirement. Standard machining involves a standard mold and EDM means a precision part with an open end. CNC machining can also be used to build more complicated moulds. The number of cavities in a mould affects its cost. More cavities in a mold require more tooling work. Branched runners are more durable than simple plastics.